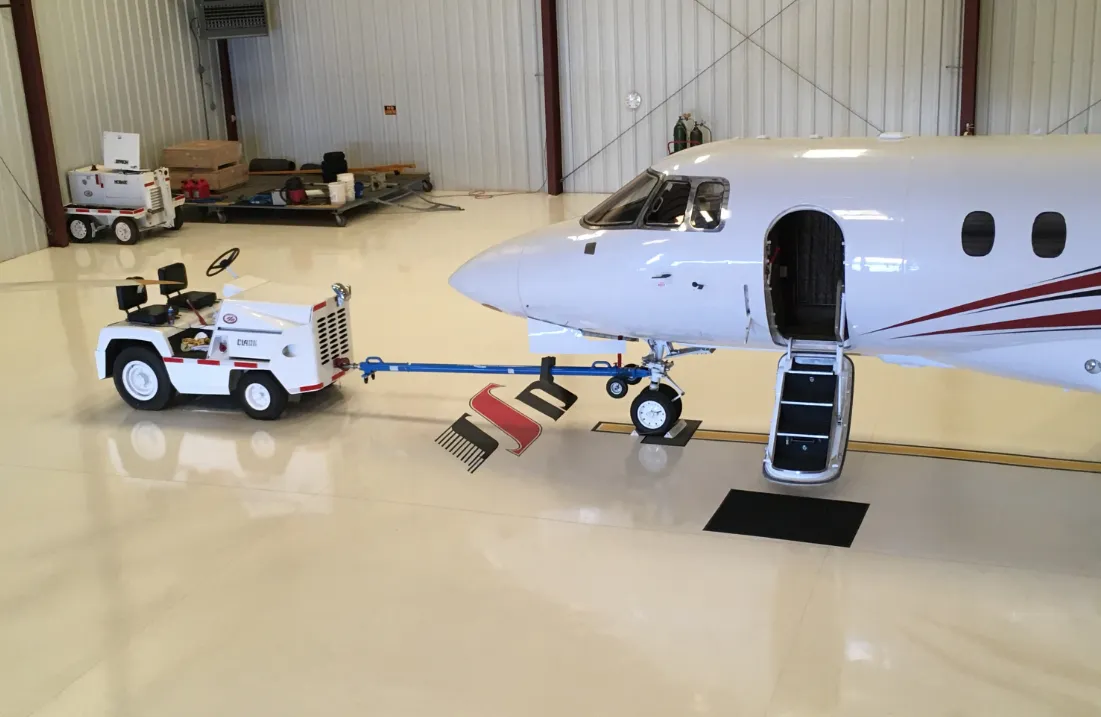
How Do Maintenance Teams Ensure the Durability of Aircraft Towbar Heads?
Aircraft towbar heads must be durable to ensure airport safety and efficiency. These crucial parts move big airplanes; therefore, dependability is critical. Towbar heads provide safe transportation from international airports to private airfields. Durability necessitates meticulous attention to detail, diligent maintenance, and a deep understanding of wear and tear variables. Each towbar head faces extreme loads, ambient conditions, and operations. Proper maintenance extends equipment life and reduces ground-handling incidents.
Careful Material Selection:
The first step in building a robust towbar head is choosing materials that can survive the demands of the aviation environment. The ideal option is high-strength steel alloys, which are well-known for their remarkable tensile strength and resistance to deterioration. Carefully forged and heat-treated to improve their mechanical qualities, these alloys are guaranteed to withstand the many loading and unloading cycles typical of ground operations.
Aircraft towbar heads are made of durable materials with fine features incorporated into the design. The head’s architecture is designed to disperse stress uniformly, avoiding concentrated areas of stress that can cause an early failure. To further prolong its life, the towbar head’s surface finish is painstakingly polished to reduce wear and friction.
Meticulous Engineering:
Towbar heads are manufactured using cutting-edge machinery and meticulous craftsmanship.. All components are guaranteed to have exact tolerances and constant quality thanks to computer numerical control (CNC) machining. A flawless fit with the aircraft’s towbarless towing system is ensured by the towbar head’s intricately sculpted curves.
Strict QC procedures are used throughout the manufacturing process to detect and resolve any problems or departures from the standard. Non-destructive testing methods, including magnetic particle and ultrasonic examination, are used to find internal faults that might jeopardize the towbar head’s structural integrity.
Strict Inspection Procedures:
Maintenance staff use exacting inspection procedures to monitor the state of towbar heads and spot any indications of wear or damage. Visual examinations are frequently carried out to find corrosion, deformation, and surface cracks. Dimensional inspections are also carried out to guarantee that the towbar head stays within the permitted tolerances. Advanced inspection methods, such as dye penetrant examination and eddy current testing, are used to find surface and subsurface fractures that may not be apparent to the unaided eye. These examinations are especially important for towbar heads that work in challenging conditions, including those exposed to de-icing chemicals or very high temperatures.
Preventative Maintenance Methods:
Maintenance personnel use proactive maintenance techniques to prevent towbar heads from wearing out too soon. Lubrication, which lowers friction between the aircraft’s towbarless towing system and the towbar head, is an essential part of this procedure. High-performance lubricants designed to endure high pressures and temperatures provide the best lubrication.
Wear components, such as bushings and pins, are routinely examined and changed as necessary to keep the towbar head operating smoothly. In addition, the towbar head is cleaned on a regular basis to get rid of dirt and debris that might hasten wear.
Data-Driven Insights:
The introduction of digital technologies has completely changed how maintenance workers oversee the towbar head’s lifetime. Real-time data on operational parameters, including temperature, load, and vibration, is gathered via sensors integrated within the towbar head. Finding trends and patterns in this data can help analyze it in order to spot any problems before they become total failures.
Based on past data and current operating circumstances, machine learning-powered predictive maintenance algorithms can estimate how much usable life is left in towbar heads. This makes it possible for maintenance crews to plan out repairs ahead of time, reducing downtime and maximizing resource use.
Ongoing Enhancement:
Maintaining towbar heads to the highest standard is a continuous effort. Maintenance teams work together to create innovation, discuss best practices, and exchange expertise with manufacturers, airlines, and regulatory agencies. Because of this cooperative approach, maintenance procedures are continually enhanced to satisfy the changing needs of the aviation sector.
Conclusion
The longevity of aircraft towbar heads is due to the maintenance crews’ continuous dedication and thorough techniques. These unsung heroes ensure that airplanes operate safely and effectively on the ground using a mix of material selection, precise engineering, stringent inspection regimes, proactive maintenance practices, data-driven insights, and continual improvement. The need to preserve towbar heads’ toughness will only increase as the aviation sector develops, reaffirming their function as the apron’s quiet protectors.