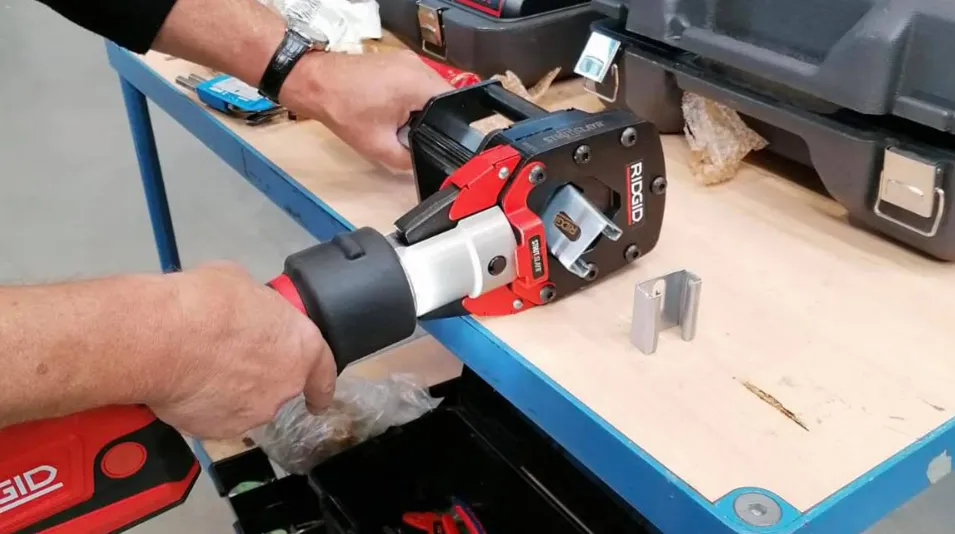
How to Make Strut Channel Using a Tube Laser Cutter?
In the current superior manufacturing panorama, precision and performance are paramount. Using modern machines, such as a tube laser cutter, can greatly streamline use. This is especially true when making strut channels. This article will look at making strut channels using a tube laser cutter. It gives a complete guide for beginners and experts.
Introduction to Strut Channel and Tube Laser Cutting
Strut channels are referred to as “strut.” They are structural parts used in the introduction and electric-powered installations. They offer useful resources for various components, including pipes, conduits, and cable trays. In the past, strut channels were made using slow guide strategies like sawing or drilling. These methods often led to errors.
Enter the tube laser-reducing era. It’s a revolutionary method with unique, green, and flexible solutions. It’s for making metal additives and incorporating strut channels. Tube laser cutters use high-powered lasers. They cut through metal tubes with great accuracy, speed, and consistency.
Understanding the Functionality of a Tube Laser Cutter
A tube laser cutter operates on the precept of targeted laser beams that melt or vaporize fabric alongside a predetermined course. This device is called laser slicing. It allows for complex designs and precise cuts on many types of metal tubes. These include metal, aluminum, and stainless steel.
The device has many key parts. They include the laser supply, lowering head, movement device, and manipulation interface. The laser supply emits a focused beam of medium power. It is directed via the cutting head onto the material’s surface. The motion gadget actions the decreasing head alongside the tube’s duration, following the favored slicing path programmed into the control interface.
Advantages of Using a Tube Laser Cutter
- Tube laser cutters are very precise. They can handle complex cuts and tight tolerances.
- Tube laser cutting is efficient. It has high reducing speeds and quick setups. It maximizes productivity and cuts costs.
- Tube laser cutters are versatile. They can handle many tube sizes, thicknesses, and materials. This makes them suitable for many uses.
- The warm area in laser cutting is small. It makes smooth edges without burrs and a great surface finish.
- Many tube laser cutters use computerized loading and unloading. They improve performance and cut the work needed.
Step-through-Step Guide on Making Strut Channel with a Tube Laser Cutter
Preparing the Material
Before planning tube laser reduction, ensure the metal tubes are flat. They should also be clean and free from defects. Knowing about fabric is key. It helps you get the gold standard, reduce harm, and cut waste.
Setting Up the Tube Laser Cutter
Next, put together the tube laser cutter by way of checking all additives for any signs of harm or put on. Ensure that the device is nicely calibrated and aligned to ensure accurate cuts. Follow the manufacturer’s guidelines for tool setup and protection strategies.
Loading the Design File
You use specialized CAD/CAM software. You lay the strut channel format regularly. You use the popular specs. Once the layout is finalized, move the record to the tube laser cutter. Use its control interface. Check the dimensions, angles, and special parameters. Make sure they work with the material and slicing method.
Adjusting Cutting Parameters
The cloth’s type, thickness, and desired cutting quality determine the cutting parameters. These include the laser’s power, the cutting speed, and the assist gas pressure. Fine-tuning those parameters is important. It makes cutting more efficient and reduces fabric waste.
Initiating the Cutting Process
The cloth is loaded and the reducing parameters are set. Provoke the lowering system by using the tube laser cutter’s control interface. Closely watch the shrinking development. Make sure the machine runs smoothly and always during the whole process.
Safety Precautions to Consider
- Protective Gear: Always placed on suitable private protective machine (PPE), together with protection glasses, gloves, and ear safety.
- Ventilation: Ensure precise, sufficient air waft in the workspace to remove fumes and gases generated during laser cutting.
- Machine Safety: Familiarize yourself with the tube laser cutter’s safety abilities and emergency protocols to prevent injuries and accidents.
- Material Handling: Handle metallic tubes carefully to avoid sharp edges and potential dangers. Use lifting gadgets or help while managing heavy materials.
Common Mistakes to Avoid
- Incorrect Material Alignment: Ensure the right alignment of the fabric in the tube laser cutter to prevent misalignment and reduce errors.
- Neglecting Maintenance: Study the tube laser cutter often. This will save you time and ensure top performance.
- Always follow safety suggestions and protocols. This will lessen the danger of accidents at work.
- Ignoring Material Specifications: Use the right cloth type and thickness. These are endorsed for tube laser cutting. They avoid processing issues and subpar effects.
Maintenance Tips for Tube Laser Cutters
- Clean the gadget additives regularly. Keep them free of particles to prevent buildup and maintain accuracy.
- Apply lubricants to moving parts. Do so as recommended by the manufacturer. This reduces friction and increases part lifespan.
- Calibration is key. Do it often to keep the tube laser cutter’s cutting performance high and consistent.
- Replace worn or broken parts right away. This will save you downtime and keep productivity.
Future Trends in Tube Laser Cutting Technology
The era of tube laser cutting is still improving. Ongoing efforts focus on making it faster, more precise, and more automated. Future developments may consist of:
- AI and Machine Learning are integrated. AI algorithms can adjust parameters in real-time. This improves performance and makes it better.
- Enhanced Automation will feature fully computerized tube lasers. They will lower structures and have robotic loading and unloading. This will further streamline production strategies.
- Advanced tube laser cutters may also have extra axes of movement. These axes give them more flexibility and versatility for cutting complex shapes.
Conclusion
Tube laser cutting has revolutionized strut channel and metal component fabrication. It provides unmatched precision, performance, and versatility. The article gives a step-by-step guide. It also covers protection precautions and best practices. By following them, producers can use tube laser cutters to improve their production and get great results.